Understanding Coating Technologies: Which One is Right for Your Tools?
Practical tips to maximize tool performance, reduce wear, and save costs in high-demand machining environments.
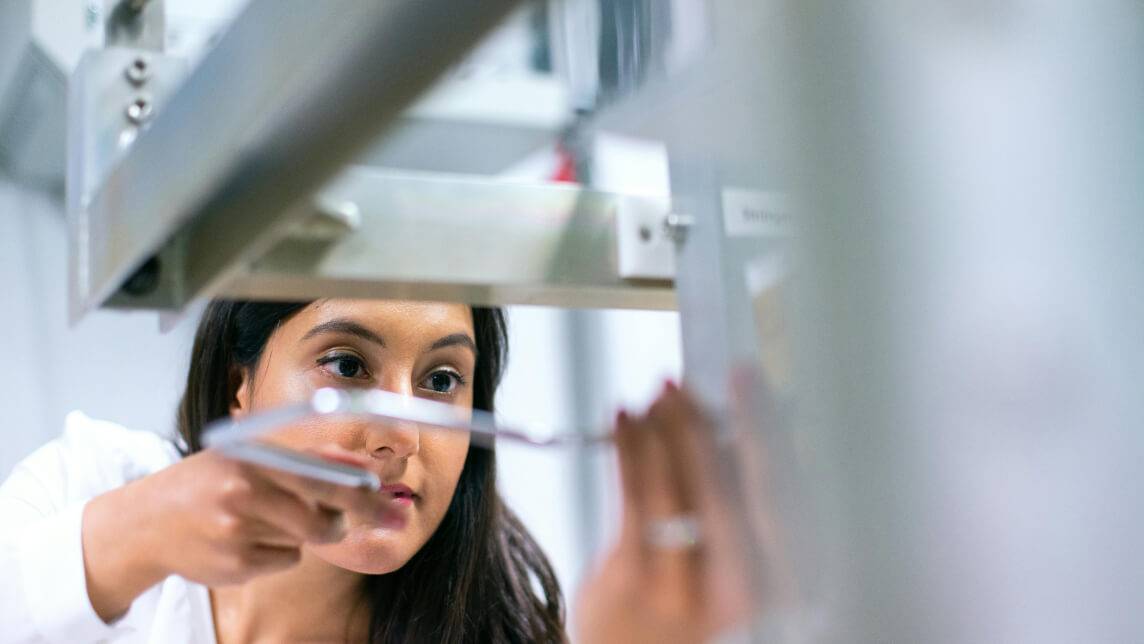
Optimise Cutting Parameters
Selecting the right cutting parameters, such as speed, feed rate, and depth of cut, is crucial for extending tool life. Running tools at excessive speeds can cause overheating and premature wear, while too slow speeds may result in inefficient material removal. Start by consulting manufacturer recommendations and fine-tuning based on the specific material and application. Regularly monitoring performance and making adjustments ensures tools operate within their ideal range, leading to improved durability and efficiency.
Use Advanced Tool Coatings
Investing in tools with advanced coatings, such as TiAlN or diamond-like carbon, can significantly enhance tool longevity. These coatings provide superior resistance to heat, wear, and corrosion, making them ideal for demanding applications like machining hardened steel or titanium. By reducing friction and dissipating heat more effectively, coated tools perform better and last longer, even under high-stress conditions. Evaluate the coating options available for your application to gain a competitive edge.
Maintain Proper Coolant and Lubrication
Effective cooling and lubrication are essential for reducing heat buildup and friction during machining. Properly applied coolant not only protects the tool but also ensures smoother cutting and prevents material adhesion. Regularly check coolant flow, concentration, and cleanliness to maintain optimal conditions. For certain applications, such as high-speed machining, using mist or air-based systems can be an effective alternative to traditional liquid coolants.