Annual carbide costs reduced by £9,600 – annual batch costs reduced by £10,700
Working with its customer when machining a 5” gate using Inconel 625 on a Dahlih MCH-630 Helix Tools was able to find time and cost savings through a simple new product recommendation.
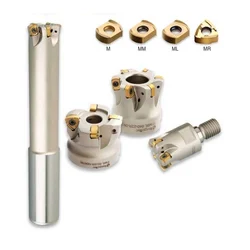
The challenge
A manufacturer of bespoke, precision engineered components for critical industries, the company was producing a 5” gate component for one of its global clients using a Stellram 125mm high feed cutter running at 30m/min and 11”/min feed as standard but felt they could improve the process to keep up with the demand.
The solution
A Helix Tools application engineer proposed that the improved productivity needed, and some additional cost savings, could be achieved by changing to a Taegutec 125mm High Feed Cutter. Due to the Teagutec inserts containing Ruthenium they are very hard and provide excellent wear. Despite containing Ruthenium the proposed insert were less expensive than those formerly used.
The result
Using their many years of experience, Helix Tools helped the CNC operators source and trial the new product. As a result of using the new inserts the process is running at an improved 31.4m/min with a 13”/min feed rate, saving 20% of machine time while annual carbide costs have been reduced by £9600 thanks to an increase in tool life from four off parts to eight off parts and annual batch costs reduced by £10,700.